The Importance of Precision Injection Molds in Electronics and Medical Supplies
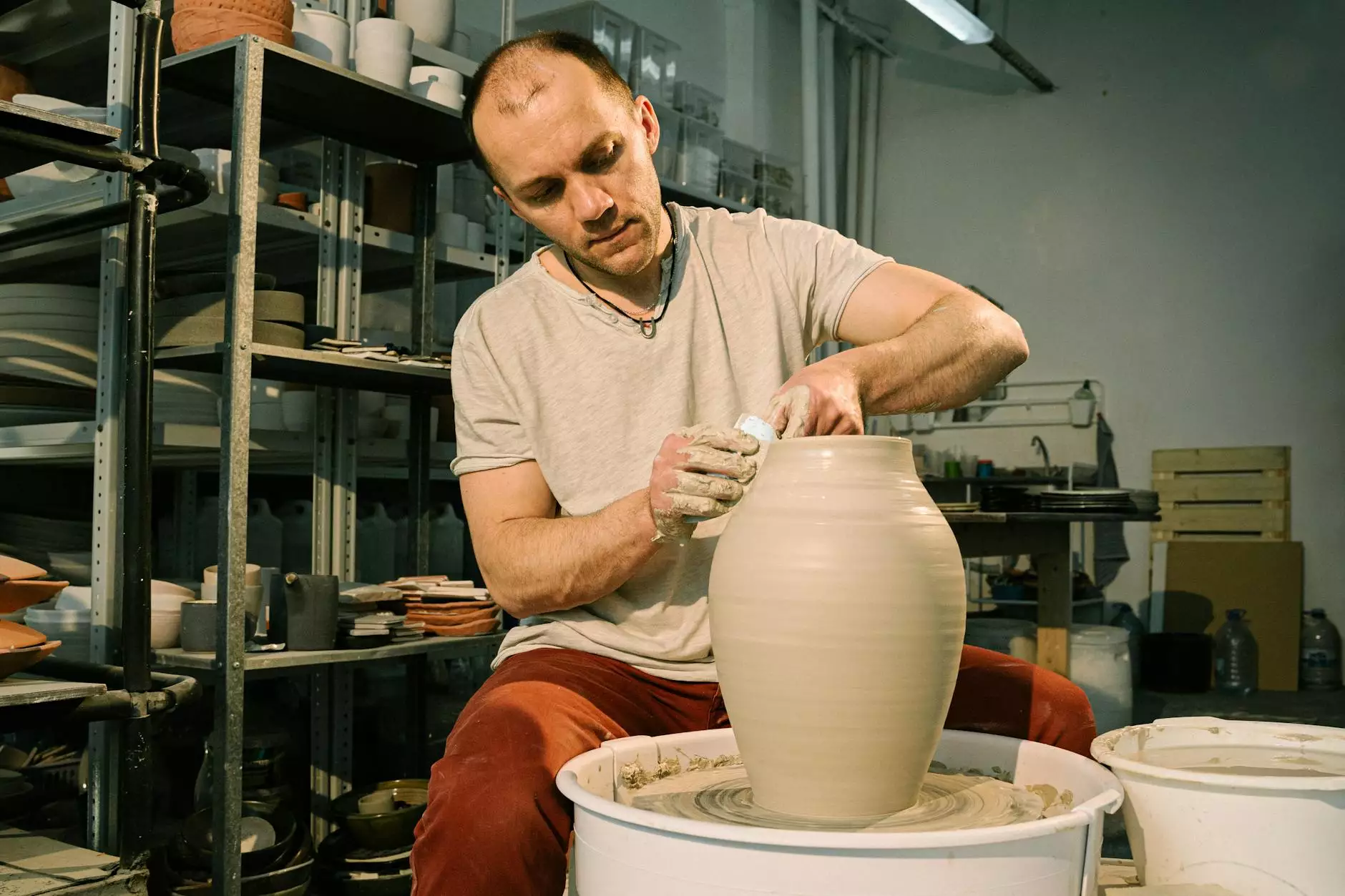
Precision injection molds play a crucial role in various industries, particularly in the fields of electronics and medical supplies. These highly engineered tools are essential for the manufacturing of parts that require strict tolerances and superior quality. In this article, we delve deep into the intricacies of precision injection molds, exploring their importance, benefits, and the future they hold in these critical sectors.
Understanding Precision Injection Molds
At its core, a precision injection mold is a tool used to create plastic parts by injecting molten plastic into a mold cavity. The precision comes from the ability to produce parts with extremely tight tolerances, which is essential for applications that demand flawless functionality.
Key Features of Precision Injection Molds
- High Dimensional Accuracy: These molds can achieve tolerances as close as ±0.01mm.
- Durability: Made from high-quality steel or aluminum, these molds are designed to withstand repeated use.
- Complex Geometries: Capable of producing intricate designs that are often impossible with other manufacturing methods.
Applications in Electronics
The electronics industry relies heavily on precision injection molds for the production of various components, such as housings, connectors, and circuit boards. As electronics continue to get smaller and more complex, the demand for high-precision components has surged.
Benefits of Precision Injection Molds in Electronics
- Improved Performance: The accuracy of molded parts ensures that electronic devices function reliably under diverse conditions.
- Cost Efficiency: High-speed production reduces the cost per unit, allowing for competitive pricing in the market.
- Scalability: Precision injection molds can be used for low-volume prototyping or high-volume production, making them versatile for manufacturers.
Applications in Medical Supplies
In the medical sector, the importance of precision is paramount. Medical devices and components must meet stringent standards for safety and efficacy, which is where precision injection molds come into play.
Ensuring Quality and Compliance
Medical parts produced using precision molds must comply with regulations such as FDA standards. This compliance assures that the components used in medical devices do not only perform their intended functions but also do so safely.
- Reduced Risk of Contamination: Exact manufacturing processes minimize the risks associated with contamination during production.
- Consistency: Each part produced is identical, ensuring reliable performance across all manufactured devices.
- Rapid Prototyping: Precision molds can be designed quickly, allowing for the swift testing of medical devices.
The Manufacturing Process of Precision Injection Molds
Creating a precision injection mold involves several meticulous steps, each contributing to the overall quality and effectiveness of the final product.
Step 1: Design and Engineering
The first step in producing precision molds is the design phase. Engineers use advanced CAD software to create detailed designs that account for the specific requirements of the product. Factors such as material selection, cooling channels, and mold cavity shapes are meticulously analyzed.
Step 2: Material Selection
The choice of materials for the molds is critical. High-grade steel is often chosen for its strength and durability, while aluminum may be selected for lighter, less demanding applications. The material must be resistant to wear, corrosion, and thermal stress.
Step 3: Machining
Advanced machining techniques, including CNC (Computer Numerical Control) machining, are employed to achieve the intricate details specified in the design. This step requires precise equipment and skilled operators to ensure accuracy.
Step 4: Assembly
Once all components are machined, they must be assembled with extreme precision. Any misalignment at this stage can affect the mold's performance and the quality of the parts produced.
Step 5: Testing and Quality Control
Before the mold is put into production, it undergoes rigorous testing to ensure it meets all design specifications and tolerances. Quality control measures help catch any issues that could lead to defects in the final product.
The Economic Impact of Precision Injection Molds
The use of precision injection molds in both the electronics and medical supply industries significantly impacts the economy. By promoting efficient manufacturing processes, these molds create jobs, enhance production capabilities, and foster innovation.
Job Creation
The demand for skilled labor to design, manufacture, and maintain precision molds drives job creation in engineering, manufacturing, and quality assurance roles.
Boosting Innovation
With the ability to create complex and precise parts, companies can innovate faster. The medical and electronics landscapes continuously evolve, making the role of precision molds crucial for staying ahead.
The Future of Precision Injection Molds
The future of precision injection molds appears bright, with ongoing advancements in technology driving improvements in material science, mold design, and manufacturing processes. Emerging technologies, such as 3D printing, are expected to complement traditional methods, leading to even more precise and adaptable manufacturing solutions.
Integration of Smart Technologies
As Industry 4.0 gains momentum, the integration of smart technologies such as IoT (Internet of Things) into the molding process will enhance efficiency. Real-time monitoring will allow manufacturers to make immediate adjustments, ensuring the highest quality outputs.
Sustainability in Manufacturing
In response to global sustainability challenges, the industry is moving towards greener practices. Precision injection molds can play a role in reducing waste and improving energy efficiency in manufacturing processes.
Conclusion
In conclusion, the role of precision injection molds in industries like electronics and medical supplies cannot be overstated. By providing superior quality, efficiency, and safety, these molds are integral to the success of modern manufacturing. As technology continues to advance, the potential for innovation and improvement in this field is limitless, promising a future where precision and quality are standard across all industries.